GENERAL DESCRIPTION
|
An Allied brochure on Foamed
Concrete is Available for
Downloading in
.pdf Form - |
May, 2014 |
1. Allied Foam Tech has been
awarded by USCA as the best chemical machinery & equipment
manufacturer in Montgomeryville, Pennsylvania in 2009-2011, 2013
& April, 2014. |
2. May, 2014- Our
innovation (click here for details) on "Wood-like Flexible Cementitious Foam"
received silver medal of the 2014 Edison Awards and we are joining
the rank of winners like Apple, 3M, Boeing, and other current
and past winners.
Edison Awards will promote Allied's innovation to a wide
variety of business press and media outlets. |
|
HUMIDITY
RESISTANT FOAM GYPSUM CEILING TILES |
Moisture & Humidity Resistant Foam Gypsum Ceilings by Client Using Allied Licensable
Cross-linking Foam Technology |
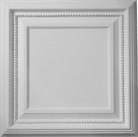 |
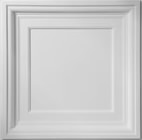 |
 |
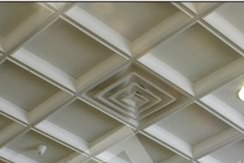 |
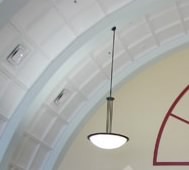 |
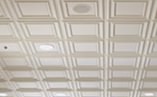 |
1.5-1.7 lbs./ft2 at 1/2" thick with acoustic
& fire resistance properties
|
FLEXIBLE CEMENT PANELS, FLEXIBLE CEMENT SHINGLES &
FLEXIBLE CEMENT BOARDS |
TECH LICENSE
OPPORTUNITIES
(January, 2014) |
Allied Foam Tech, through its ~ 20 years
of internal R & D effort and global industrial
experience in building trade, has developed a wide range
of proprietary lightweight building composites, process
and performance properties based on its patent pending
lightweight fiber cement technologies and composites.
Major building product manufacturers interested in
licensing rights
please click here. |
A few highlights are given below: |
·
1.
Superlight and flexible cement sheets
with great adhesion characteristics, high water
resistance, and high impact and compressive strengths
(MOR > 750 psi, indented compressive strength >
1,000 psi and 24 inches static water column test > 48
hours).
·
2.
Lightweight and flexible (roll forming)
decorative sheetings for various exterior or interior
wall wrap or wall covering applications.
·
3.
Asphalt-free flexible
shingle (110-130 mils) and underlayment materials (50 to
70 mils) with UV resistance, freeze-thaw stablility,
great coating and granule adhesion, tear strength and
lightweight that is not available in the current roofing
industry.
·
4.
Foamed curable thin
sheets, with their uv stability, flexibility, high
tensile strength, great adhesion to metal and water
resistance, are very adaptable for the manufacture of
roofing shakes and metal roof tile composites.
·
5.
Lightweight flexible
cementitious coatings for the various commercial foam
boards such as polystyrene and polyurethane foam boards.
·
6.
Lightweight cast stones
with high mouldability (low slump), good fire resistance
and quick demolding behavior, high tensile strength and
adhesion for pigment and coloring should be very
suitable for direct replacement of the various heavy
stone or other concrete cast stone products.
·
7.
The flexible
cementitious composites allows prefabricated or cast in
place sandwich panels of various kinds to be made.
Extrudable cementitous composites can also be engineered
allowing for friendly adaptation of the various
manufacturing process, curing and storage capabilities. |

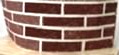
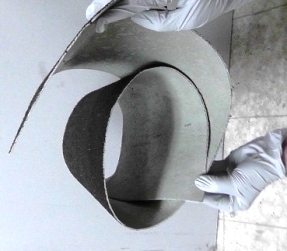

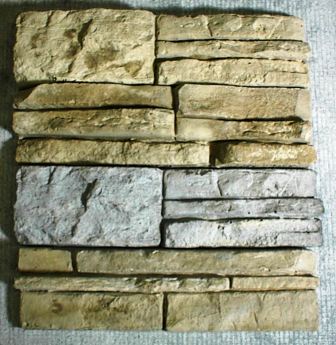
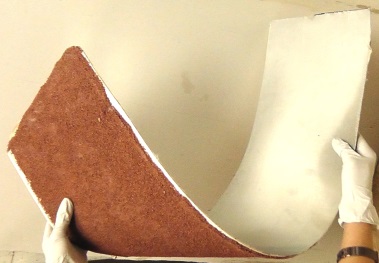 |
|
|
ACOUSTIC CEMENT PANELS,
WATER PERMEABLE FOAMED CEMENT & FOAMED CONCRETE |
Click here
for QuickTime
Nov., 2014
The world's first foam cement and concrete with control
of % Open POREs vs Close POREs
*
economical porous material for all weather acoustic
panels *
*
WATER PERMEABLE FOAM CEMENT AND FOAM CONCRETE *
(acoustic
panels for highway, mine, tunnel, railroad, mass
transit, power plant, subway, marine vessel, airport,
heat pump) |
Mostly Open Pores |
Mostly Closed Pores |
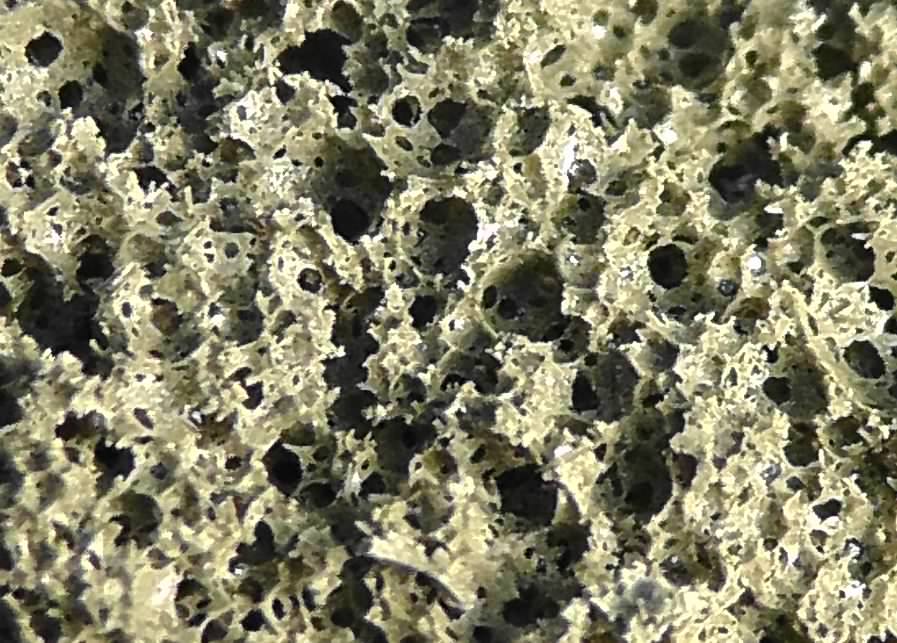 |
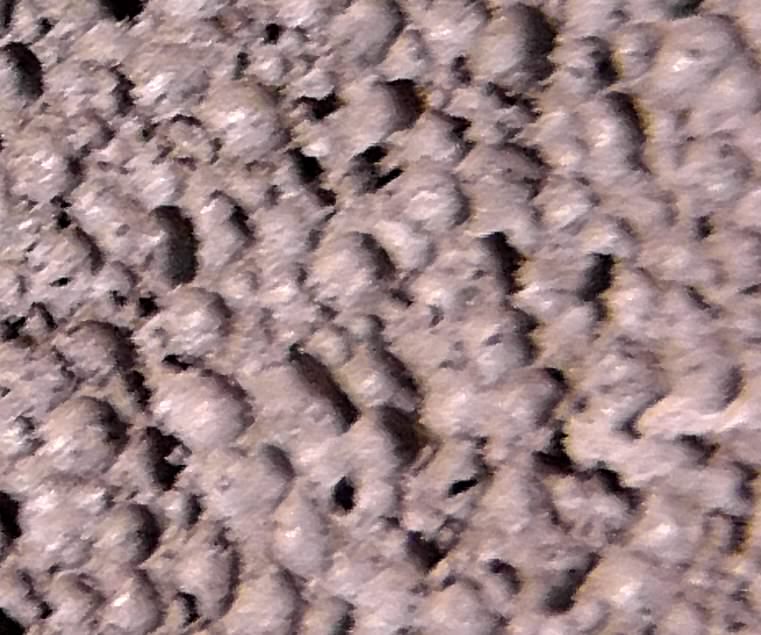 |
|
Click here
for QuickTime
Nov., 2014 |
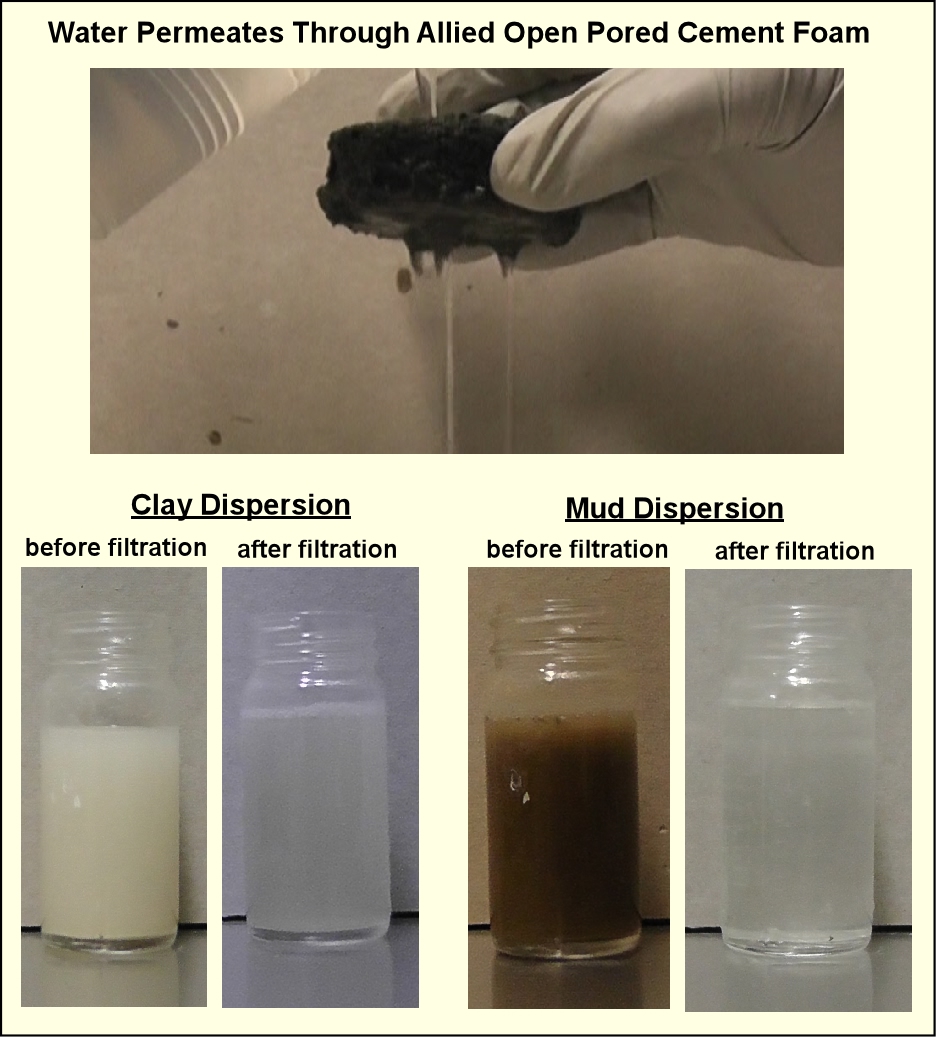 |
Such
foam cement can easily reach a compressive strength of >
270 psi at an air dried density of 29 pcf. |
*All the commercial
pervious lightweight cement systems rely their
permeability on either the very coarse open pores or the
interconnected capillaries derived from severe foam
collapse. Such cellular cement composites are typically
very low in compressive strength, e.g. 80 - 150 psi at
densities ~ 30 pcf. |
Foam concrete or lightweight concrete derived from Allied's
aqueous foams are suitable for both
precast and
cast-in-place
applications. Some of the highly insulative cementitious
foams at densities 48 kg/m3(3 pcf) to 645 kg/m3(40
pcf) or higher can be used as block fills, lightweight roof deck
and void-fill materials. Good strength characteristics with
reduced weight make lightweight concrete based on Allied's
aqueous foams suitable for structural and semi-structural
applications such as lightweight partitions, wall and floor
panels, and lightweight blocks. Cementitious foams derived from
Allied's premium systems are suitable for thin layer coating
applications where specific performance criteria are required.
Foamed concrete and foamed cement made with Allied's foam have very fine
pore structure, unlike that made with conventional proteinaceous and
surfactant foams. The pore structure of Allied's foams hardly show any
sign of deterioration as the density of the foamed cement decreases to
below 160 kg/m3 (10 pcf). At densities below 160 kg/m3,
the pore texture of foamed cement derived from conventional foam agents
becomes so coarse that most of them show severe structural collapse.
The dynamic nature of Allied foam systems allows different foam rheology
to be incorporated into the host cement/concrete matrix to satisfy a
wide range of slump loss requirements.
The inert nature of Allied foam
systems makes them
compatible with different kinds of aggregates, fillers,
extenders, retarders, accelerators, colorants, hydraulic
inorganics and many other additives. |
|
|
|
Allied Low Slump CEMENT Geofoam/GEOTECHNICAL
FILL - A GAME CHANGER
in
the Geofoam MarkET |
Allied "Cement Geofoam"
will greatly simplify the application and cost relative
to the "Expanded Polystyrene Geofoam" |
Highway Embankment, Bridge Underfill, Landscape
Architecture, Slope Stabilization, Levees, Airport
Runway, Road Construction |
Allied 5-15 pcf Fiber Low Slump Cement Geofoam |
Conventional 0.7 - 2 pcf EPS Geofoam |
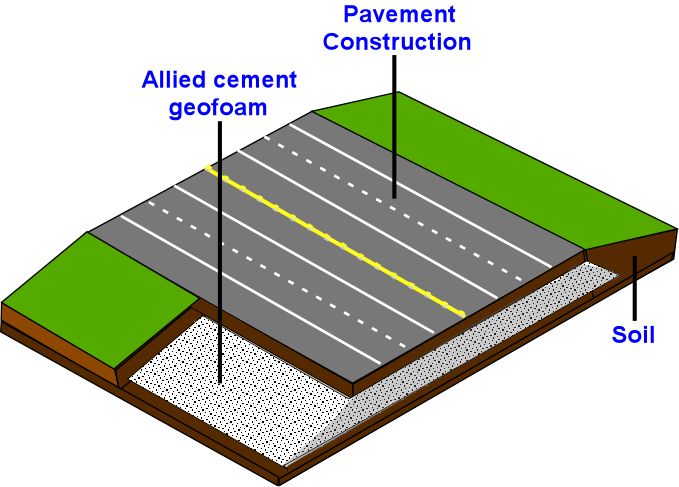 |
> |
>> |
> |
Low load on the
surrounding soil |
Low load on the
surrounding soil |
Casting with a continuous low slump pour |
stacking of
individual blocks delivered on site |
Shape & conform
to the landscape easily with the low slump cast |
Shape & conform
to the landscape easily with the precast blocks |
Foam formation onsite
through compressed air and foam agent |
Huge number of
eps blocks have to be delivered on site |
No fire hazard,
good solvent resistance |
Fire hazard,
lack of solvent resistance(membrane needed) |
Intimate soil
contact with easy surface leveling and slope build-up |
Sand leveling
or other means needed for block alignment |
Uniform and
bulk cast without gap formation or concerns for
buoyancy, individual piece heaving/floatation
|
Geomembrane or
separation layer needed to avoid uneven block floatation
or dissolution by organic liquid seepage. |
Uniform &
continuous pour/cast with ease of contour buildup
|
Interblock
locking plates may be needed for block alignment |
Wide range of
density and strength possible:5 - 50 pcf, 2 >500psi |
Density and strength are limited - 0.6 - 2.0 pcf, 2-10
psi. |
For more details click here. |
Allied Low Slump Cementitous
Geofoam - easy to shape & conform to the landscape
without moulds |
Cast w/o
Mould - Wet |
Cast w/o
Mould - Dry (d=25 pcf) |
Mould-free
Cast- Wet |
Mould-free
Cast - Dry (d=8 pcf) |
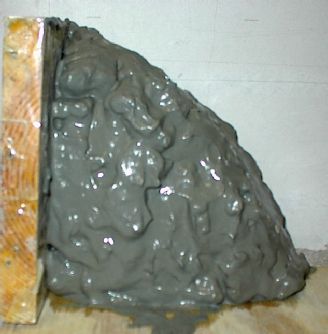 |
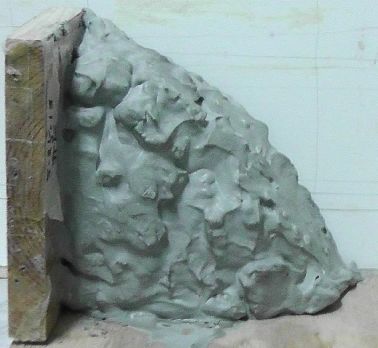 |
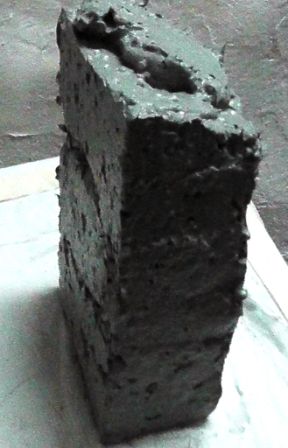 |
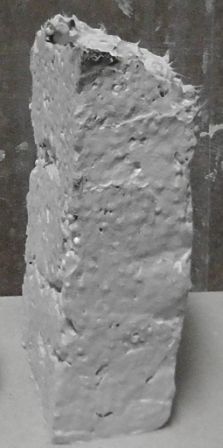 |
Fiber
Re-enforced Allied Cement Geofoam vs EPS Geofoam - Very
Comparable Toughness During Compression |
 |
* Higher
compressive strength can easily be reached by a slight
density increase of Allied Cement Geofoam, e.g. 85 psi
at a density of 16 pcf. |
|
|
November, 2013 |
GEOPOLYMER FOAM
|
Density = 2.9 pcf (47 kg/m3),
R Value = 3.84 ft2oFh/(Btu in) |
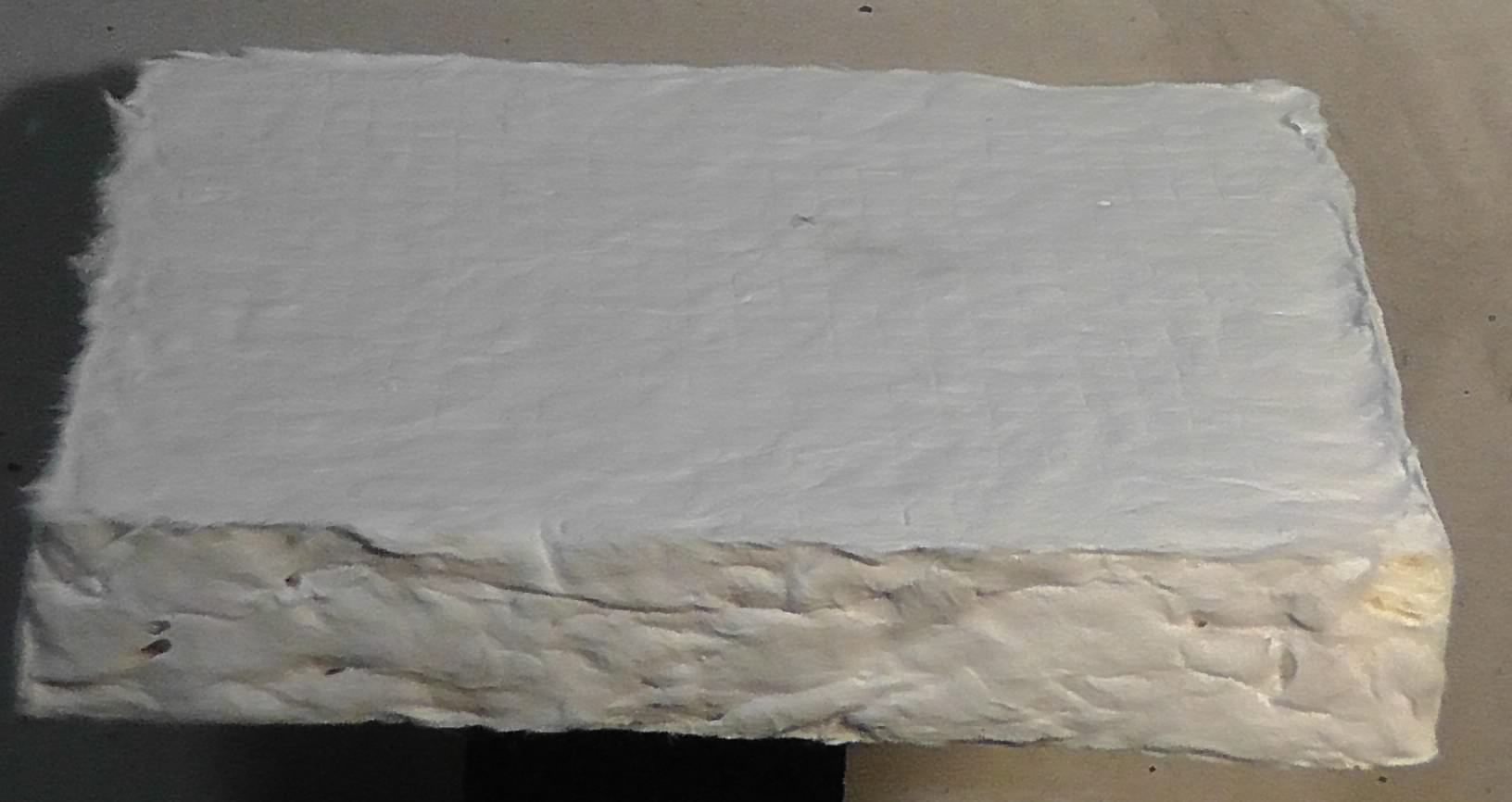 |
Highlights
on Allied’s WORK with Foamed DECORATIVE STONES,
Blocks and Foamed Panels
|
(WE
PROVIDE FOAM PRODUCTS, FOAM MACHINERY AND TECH SERVICE IN
PROCESS & MIX DESIGNS) |
Autoclaved aerated
concrete (AAC) was introduced in Europe over half a
century ago as a lightweight construction material. The key
features AAC has over conventional foamed concrete are significantly better strength and lower shrinkage/cracking.
However, most of the attempts over the last few decades to
introduce AAC to the US either failed or hardly made any signifcant
impact to the construction industry. The million of dollars of capital investment needed for
the manufacture of AAC over the
conventional precast plant is just one of the many reasons
reported in the literature. |
Freshly
prepared decorative stone panels with low shrinkage and
non-cracking features are shown below: |
3.6
feet x 2.6 feet (1.1 meters x 0.8 meters) |
Total
weight = 28 pounds or 12.7 kg. |
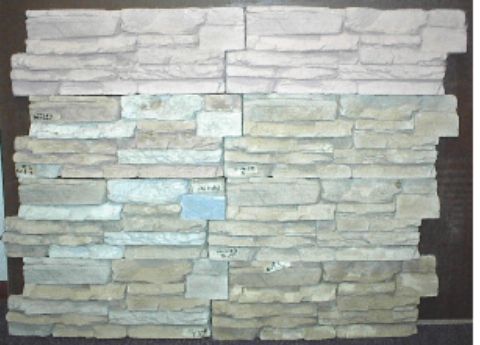 |
(the
blue center block was acid-etched showing the blue
decorative sand texture underneath) |
|
Dimensions
of individual panel = 22" x 8" w. thickness of
0.25"-1.25" (0.56meter x 0.2meter w. thickness of
1.6cm-3.2cm) |
(weight
per panel = 3.5 pounds (1.6 kg.) |
|
|
Extrudable Foam Cement Blocks |
Freshly prepared
cement/aggregate bricks/blocks derived from Allied's specialty foams
with high slump loss may even be extrudable and thus amenable for
mass production. A freshly cast foam brick at 37 pcf (600
kg/m3) without using any mould is shown below: |
Freshly
Made Foam Cement Brick w. High Slump Loss (density = 37
pcf) |
Extruded
Foam Cement/Ltwt Aggregate Composite (density = 40 pcf,
compressive
strength = 660 psi (4.6 MPa)) |
Instantly
Demolded Cement/Ltwt Aggregate Composite (density = 31 pcf,
compressive
strength = 460 psi (3.2
MPa)) |
(a
mould-free cast) |
(low
pressure extrusion) |
(demolded
in < 1 minute) |
|
|
|
|
Highlights
on Allied’s WORK witH Geotechnical engineering, LANDSCAPE ARCHITECTURE AND SLOPED ROOF
DECK |
Composites with
Allied’s premium foamed cement/high
slump-loss/high strength 35 pcf foamed cement allows greater and
simpler landscape architecture and roof deck designs not achievable
by any conventional cellular concrete.
1. Geotechnical Engineering &
Landscape architecture
A. conventional
cellular concrete - conventional 35 pcf LDCC
(Low Density Cellular Concrete) with
shaved expanded polystyrene blocks.
Very limited slope
negotiation for conventional cellular concrete – less than
˝ inch drop per 10 feet span. |
Geofoam/styrofoam blocks
of various sizes/shapes are needed to create artificial
slopes. |
Labor intensive and slow
process. |
B. New and flexible
designs with Allied’s high
slump-loss foamed cement
^ back to top
Highly sloped landscape with > 1 feet drop per 10 feet span can
easily be achieved. |
The use of Geofoam/styrofoam blocks is significantly reduced
or totally eliminated. |
Labor savings and faster process. |
High Slump
Loss Foamed Cement/Lightweight Aggregate
Composites with Low Shrinkage at a Dry Density
of 35-50 pcf (565 - 806 kg/m3) |
|
|
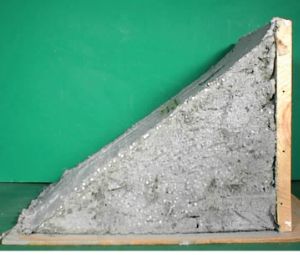 |
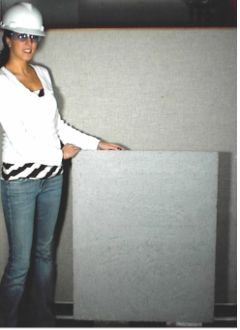 |
>
2.5 feet drop per 10 feet span (1V/4H) |
Full
Size Air Conditioner Pad From High Slump Loss/Low Shrinkage
Foamed Cement Composite |
(dry density = 35 pcf) |
(dry density = 48 pcf) |
2. Improved Foamed Cement Roof
Deck Designs
Highly sloped industrial
and residential roofdecks or roofings become possible with Allied's
high slump-loss foamed cement product and mix design.
Allied's stable foam with
high slump loss can be applied directly on corrugated metal sheets
of new or repaired roofs without foam dewatering and possible water
leakage to the interior structure of the floors underneath while
such problems have always been associated with conventional cellular
concrete roof decks.
Using Allied’s 35pcf/10 pcf foamed cement
composite as roof deck structure will
achieve the right combination of thermal insulation and light weight
like
conventional cellular concrete/styrofoam blocks but with appreciable
labor and time savings and the flexibility in roof deck designs with varied shapes
and contours not achievable before.
Comparison of
Roof Deck Composites from Allied's Foamed Cement Composite &
Conventional Foamed Cement/Expanded Polystyrene Board Composite.

|
|
|
28 DAYS STRENGTH
PROFILE AT 55 - 80 PCF (890 - 1,290 Kg/M3) -
loadbearing
and semi-structural.
|
(The following data are derived from
mix designs that may have different slump loss characteristics from
that at 30 - 60 pcf)
|
Density
(Air Dry) |
Compressive
Strength |
(pcf) |
(Kg/M3) |
(psi) |
(MPa) |
56 |
900 |
1,200 |
8.2 |
65 |
1,040 |
1,480 |
10.2 |
69 |
1,110 |
1,700 |
11.7 |
74 |
1,190 |
2,300 |
15.9 |
76 |
1,240 |
> 2,500 |
> 17.2 |
|
|
COMPOSITE BLOCKS,
PANELS
-
non-loadbearing, low-load bearing
& insulative.
|
Even at densities < 20 pcf, the
strength development of Allied's foam/lightweight aggregate
composites allows <24 hours demolding time while still
maintaining good handling characteristics (all three blocks shown
below were demolded in 18-24 hours and were immediately saw-cut to
proper size)
|
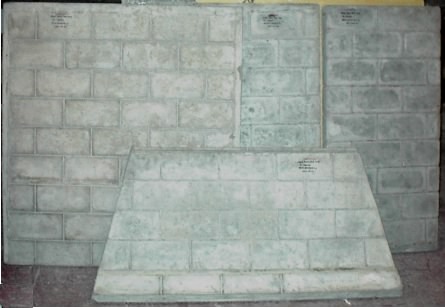 |
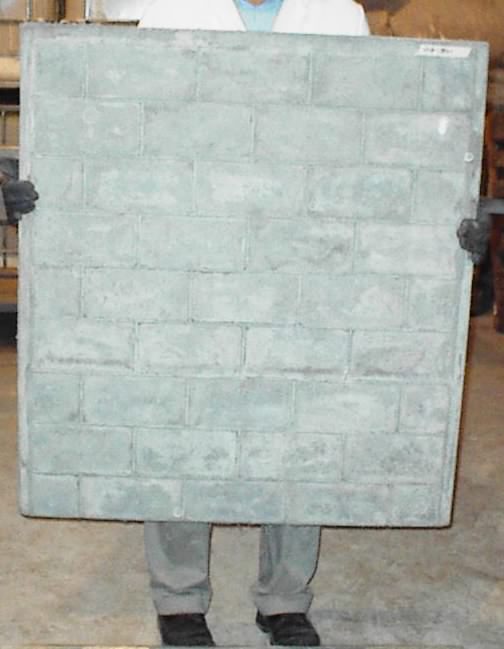 |
Fiber
Re-enforced Foam Cement Panels (50 pcf) |
Held in Air -
1.5 inch thick |
|
PERFORMANCE
Some
Performance Features of Concrete and Cement Incorporating Allied's
Foam Systems: |
Consistent and fine pore texture at different densities
Low water uptake
Hight early and 28 day compressive strengths
Good thermal and acoustic properties
Wide range of rheological, adhesive and thin-set properties
|
The excellent
stability of Allied's foam products is demonstrated in the following pictures
of lightweight cement and concrete:
|
Foamed Cement
Using Allied AFT-400
Density = 0.24 g/cc (15 pcf)
|
Foamed
Cement
Using Proteinaceous Foam
Density = 0.24 g/cc (15 pcf)
|
|
|
fine
pores
|
coarse pores
|
|
Strength Development and Water
Uptake of Foamed Cement
|
Allied foams are compatible with different kinds of cement, fly ash, sand/aggregate fillers,
retarders, accelerators and water reducers. The AFT-400 series of foam reagents provide
cement and concrete with very low water uptake. Cementitious foams at densities as low as one tenth (1/10) that of dense concrete will still maintain lower than 15%
(by volume) water uptake in a 24 hour water immersion test. |
The following table shows some typical strength and water uptake characteristics
of a lightweight cement formulation using Allied AFT-400: |
FOAMED
CEMENT FORMULATION WITH AFT-400 - Strength Development and Water
Uptake
Density of Foamed Cement
(in
gram/cm3) |
Compressive
Strength |
24
hour Water
Uptake |
After
24 Hours |
After
28 Days |
(volume/volume) |
0.74
(oven
dried) |
468
psi |
825
psi |
<
5 % |
(3.25
Mpa) |
(5.3
Mpa) |
|
|
| | | |